Heat & Cool for Plastic Injection Molding
Experience the transformative power of heat & cool technology in plastic injection molding. Optimize efficiency, reduce cycle times, and achieve superior quality with precise temperature control and advanced techniques
ROCTOOL
Increase your process window when adding Roctool to your mold.
The ability to quickly heat the mold and fully control temperature distribution opens new molding possibilities, including shorter cycle time, part quality increase and flow length extension. An immediate Return On Investment.
LIVE DEMO – 100% Recycled ABS
Roctool presented a complex case at the K-show 2016, with a decorative texture on the mold. The demonstration focused on eliminating weld lines, reduced sink marks, a quick cycle time and a full replication of tool surface. With the Roctool induction process, it is now possible to mold fully recycled ABS parts without any defects.
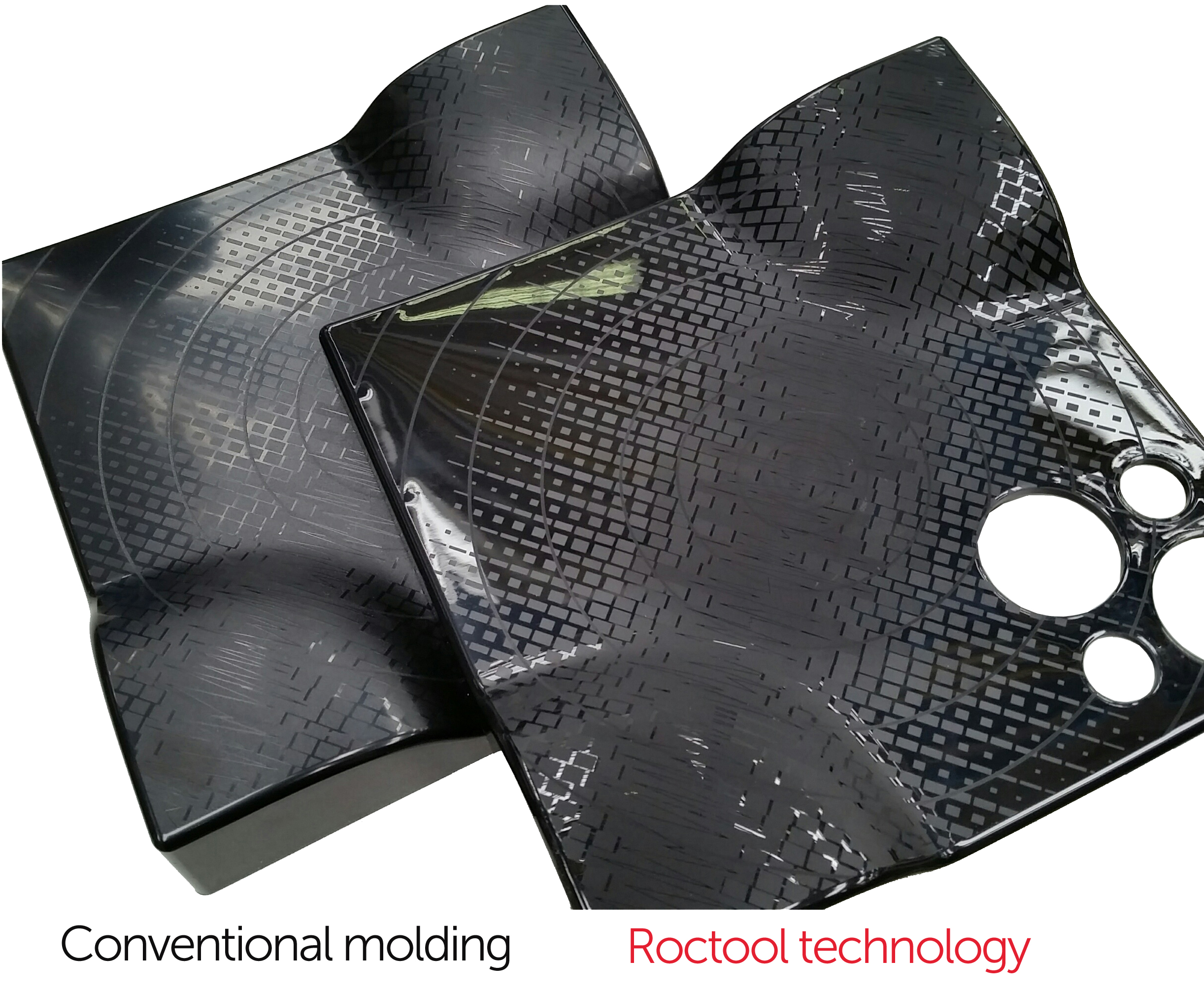
3iTech® Heat & Cool Integration
Roctool’s patented technology consists of designing a Heat & Cool layout in order to provide a fast and homogeneous heating. Flexible inductors will allow to follow any complex shape of tooling, while using any metallic alloys from standard steel to more marginal alloys as invar for dedicated applications. A high frequency current will be generated to run through the inductors, creating eddy currents and joule effect to heat up the mold surface. Using standard cooling channels with water and ensuring a fully turbulent flow rate enables efficient cooling of the tool.



Introducing HD Plastics™ – High Definition Plastics
With Roctool’s Heat & Cool molding technologies and selected materials, we set up a new standard in the industry: HD Plastics™. With Roctool high heat molding, the level of the tool surface replication goes up to 97.2%, providing product designers very premium looks, high gloss possibilities and matching the texture they initially targeted.
The flow increase with Roctool high heat molding technology unlocks design rules and pushes the limits in order to create thin wall applications.
See an overview of our performance rate database.
HD Plastics™ Advantages
Unlimited Surface Design
HD Plastics™ works with all texturing technologies including classical tool surface texturing (mirror polish, chemical, EDM etc.) and also with innovative texturing (laser etching). HD Plastics™ offers unlimited patterns and design possibilities for top surface applications & tool design support.
Tool Surface Replication
With Roctool high heat molding, the level of the tool surface replication is over 90%, compared to around 50% with conventional technologies (depending on amorphous or semi-crystalline resins) and provides product designers premium looks, high gloss possibilities and matching the texture they initially targeted.
No Molding Temperature Limitations
Without any heating limitation before injection, Roctool high heat molding technology allows to find optimal molding parameters in order to reach the best possible overall quality for commodity resins all the way to ultra-polymers.
Eliminate Secondary Operations
Planet Friendly and No Paint is a priority. With HD Plastics™ , Roctool is currently evaluating all the possible solutions to eliminate additional decoration, such as paint, varnish or film. The use of the dedicated resins with Roctool process creates unique decorated textures on the tool surface.
Increased Part Quality
The temperature control eliminates major defects such as visible weld lines, sink marks, flow lines and blush. Part mechanical properties are enhanced by reduction of frozen in residual stresses and weld line improvement. Part dimensions are closer to mold cavity design and parts standard deviation during production period induced by processing is improved.
Reduced Wall Thickness - Lightweighting
One of the main challenges in the plastic industry is to reduce the overall part thickness. The flow increase with Roctool high heat molding technology unlocks design rules and pushes the limits to create thin wall applications even for engineering resins with high viscosity.

We’re ready to work on a first feasibility
Send us a short brief for the production of your part, we’ll answer you back within the next 48 hours.
Plastic injection product examples
ROCTOOL TECHNOLOGY
Heat & Cool system
ECO-MOLDING™
Industry
Stories
Automotive, Aerospace, Electronics, Beauty, Consumer Goods, Medical
Work
with Us
Feasibility Study, Engineering, Analysis & Tool Design, Components, Installation